ویفر ڈائسنگ ٹیکنالوجی، سیمی کنڈکٹر مینوفیکچرنگ کے عمل میں ایک اہم قدم کے طور پر، چپ کی کارکردگی، پیداوار، اور پیداواری لاگت سے براہ راست منسلک ہے۔
#01 ویفر ڈائسنگ کا پس منظر اور اہمیت
1.1 ویفر ڈائسنگ کی تعریف
ویفر ڈائسنگ (اسکرائبنگ کے نام سے بھی جانا جاتا ہے) سیمی کنڈکٹر مینوفیکچرنگ میں ایک ضروری قدم ہے، جس کا مقصد پراسیس شدہ ویفرز کو متعدد انفرادی ڈائس میں تقسیم کرنا ہے۔ یہ ڈائز عام طور پر مکمل سرکٹ کی فعالیت پر مشتمل ہوتے ہیں اور یہ بنیادی اجزاء ہوتے ہیں جو بالآخر الیکٹرانک آلات کی تیاری میں استعمال ہوتے ہیں۔ جیسے جیسے چپ ڈیزائن زیادہ پیچیدہ ہوتے جا رہے ہیں اور طول و عرض سکڑتے جا رہے ہیں، ویفر ڈائسنگ ٹیکنالوجی کے لیے درستگی اور کارکردگی کے تقاضے تیزی سے سخت ہوتے جا رہے ہیں۔
عملی کاموں میں، ویفر ڈائسنگ عام طور پر اعلیٰ درستگی والے ٹولز جیسے ڈائمنڈ بلیڈ کا استعمال کرتی ہے تاکہ یہ یقینی بنایا جا سکے کہ ہر ڈائی برقرار اور مکمل طور پر فعال رہے۔ کلیدی مراحل میں کاٹنے سے پہلے تیاری، کاٹنے کے عمل کے دوران عین مطابق کنٹرول، اور کاٹنے کے بعد معیار کا معائنہ شامل ہے۔
کاٹنے سے پہلے، درست کاٹنے کے راستوں کو یقینی بنانے کے لیے ویفر کو نشان زد اور پوزیشن میں رکھنا چاہیے۔ کاٹنے کے دوران، پیرامیٹرز جیسے ٹول پریشر اور رفتار کو سختی سے کنٹرول کیا جانا چاہیے تاکہ ویفر کو نقصان نہ پہنچے۔ کاٹنے کے بعد، اس بات کو یقینی بنانے کے لیے کہ ہر چپ کارکردگی کے معیار پر پورا اترتی ہے، جامع معیار کے معائنے کیے جاتے ہیں۔
ویفر ڈائسنگ ٹکنالوجی کے بنیادی اصولوں میں نہ صرف کاٹنے والے سامان کے انتخاب اور عمل کے پیرامیٹرز کی ترتیب شامل ہے بلکہ کاٹنے کے معیار پر مشینی خصوصیات اور مواد کی خصوصیات کا اثر بھی شامل ہے۔ مثال کے طور پر، کم-کے ڈائی الیکٹرک سلیکون ویفرز، اپنی کمتر میکانی خصوصیات کی وجہ سے، کاٹنے کے دوران تناؤ کے ارتکاز کے لیے انتہائی حساس ہوتے ہیں، جس کی وجہ سے چِپنگ اور کریکنگ جیسی ناکامی ہوتی ہے۔ لو-k مواد کی کم سختی اور ٹوٹ پھوٹ انہیں مکینیکل قوت یا تھرمل دباؤ کے تحت ساختی نقصان کا زیادہ خطرہ بناتی ہے، خاص طور پر کاٹنے کے دوران۔ ٹول اور ویفر کی سطح کے درمیان رابطہ، اعلی درجہ حرارت کے ساتھ مل کر، تناؤ کے ارتکاز کو مزید بڑھا سکتا ہے۔
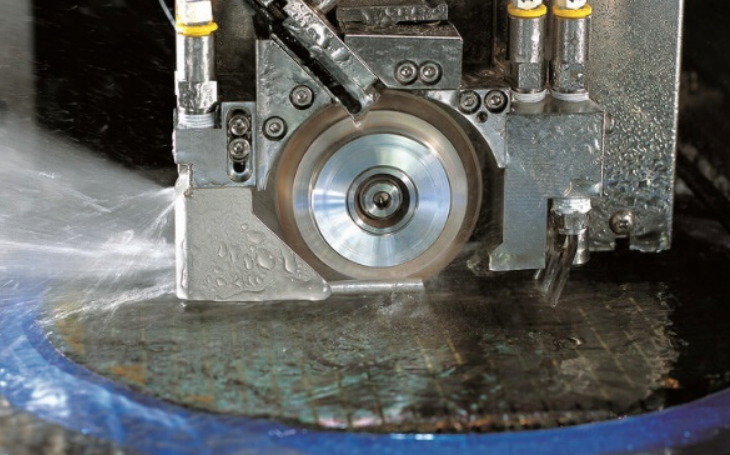
مادی سائنس میں ترقی کے ساتھ، ویفر ڈائسنگ ٹیکنالوجی نے روایتی سلکان پر مبنی سیمی کنڈکٹرز سے آگے بڑھ کر گیلیم نائٹرائڈ (GaN) جیسے نئے مواد کو شامل کیا ہے۔ یہ نیا مواد، اپنی سختی اور ساختی خصوصیات کی وجہ سے، ڈائسنگ کے عمل کے لیے نئے چیلنجز کا باعث بنتا ہے، جس میں کاٹنے کے اوزار اور تکنیک میں مزید بہتری کی ضرورت ہوتی ہے۔
سیمی کنڈکٹر انڈسٹری میں ایک اہم عمل کے طور پر، مستقبل کے مائیکرو الیکٹرانکس اور انٹیگریٹڈ سرکٹ ٹیکنالوجیز کی بنیاد ڈالتے ہوئے، ترقی پذیر مطالبات اور تکنیکی ترقی کے جواب میں ویفر ڈائسنگ کو بہتر بنایا جاتا ہے۔
ویفر ڈائسنگ ٹیکنالوجی میں بہتری معاون مواد اور ٹولز کی ترقی سے آگے ہے۔ ان میں عمل کی اصلاح، آلات کی کارکردگی میں اضافہ، اور ڈائسنگ پیرامیٹرز کا درست کنٹرول بھی شامل ہے۔ ان پیش رفتوں کا مقصد ویفر ڈائسنگ کے عمل میں اعلیٰ درستگی، کارکردگی اور استحکام کو یقینی بنانا ہے، سیمی کنڈکٹر انڈسٹری کی چھوٹی جہتوں، اعلیٰ انضمام، اور زیادہ پیچیدہ چپ ڈھانچے کی ضرورت کو پورا کرنا ہے۔
بہتری کا علاقہ | مخصوص اقدامات | اثرات |
عمل کی اصلاح | - ابتدائی تیاریوں کو بہتر بنائیں، جیسے زیادہ درست ویفر پوزیشننگ اور راستے کی منصوبہ بندی۔ | - کاٹنے کی غلطیوں کو کم کریں اور استحکام کو بہتر بنائیں۔ |
- کاٹنے کی غلطیوں کو کم کریں اور استحکام کو بہتر بنائیں۔ | - ٹول پریشر، رفتار اور درجہ حرارت کو ایڈجسٹ کرنے کے لیے ریئل ٹائم مانیٹرنگ اور فیڈ بیک میکانزم کو اپنائیں | |
- ویفر ٹوٹنے کی شرح کو کم کریں اور چپ کے معیار کو بہتر بنائیں۔ | ||
آلات کی کارکردگی میں اضافہ | - اعلی صحت سے متعلق مکینیکل سسٹمز اور جدید آٹومیشن کنٹرول ٹیکنالوجی کا استعمال کریں۔ | - کاٹنے کی درستگی کو بہتر بنائیں اور مواد کے ضیاع کو کم کریں۔ |
- لیزر کٹنگ ٹیکنالوجی متعارف کروائیں جو زیادہ سختی والے میٹریل ویفرز کے لیے موزوں ہو۔ | - پیداوار کی کارکردگی کو بہتر بنائیں اور دستی غلطیوں کو کم کریں۔ | |
- خودکار نگرانی اور ایڈجسٹمنٹ کے لیے آلات کی آٹومیشن میں اضافہ کریں۔ | ||
عین مطابق پیرامیٹر کنٹرول | - کاٹنے کی گہرائی، رفتار، ٹول کی قسم، اور کولنگ کے طریقے جیسے پیرامیٹرز کو باریک طریقے سے ایڈجسٹ کریں۔ | - ڈائی سالمیت اور برقی کارکردگی کو یقینی بنائیں۔ |
- ویفر مواد، موٹائی، اور ساخت کی بنیاد پر پیرامیٹرز کو حسب ضرورت بنائیں۔ | - پیداوار کی شرح کو بڑھانا، مادی فضلہ کو کم کرنا، اور پیداواری لاگت کم کرنا۔ | |
اسٹریٹجک اہمیت | - مسلسل نئے تکنیکی راستے تلاش کریں، عمل کو بہتر بنائیں، اور مارکیٹ کے تقاضوں کو پورا کرنے کے لیے آلات کی صلاحیتوں میں اضافہ کریں۔ | - چپ مینوفیکچرنگ کی پیداوار اور کارکردگی کو بہتر بنائیں، نئے مواد اور جدید چپ ڈیزائن کی ترقی میں معاونت کریں۔ |
1.2 ویفر ڈائسنگ کی اہمیت
ویفر ڈائسنگ سیمی کنڈکٹر مینوفیکچرنگ کے عمل میں ایک اہم کردار ادا کرتی ہے، جو براہ راست بعد کے مراحل کے ساتھ ساتھ حتمی مصنوعات کے معیار اور کارکردگی کو متاثر کرتی ہے۔ اس کی اہمیت کو اس طرح تفصیل سے بیان کیا جا سکتا ہے:
سب سے پہلے، ڈائسنگ کی درستگی اور مستقل مزاجی چپ کی پیداوار اور وشوسنییتا کو یقینی بنانے کی کلید ہے۔ مینوفیکچرنگ کے دوران، ویفرز کو متعدد پیچیدہ سرکٹ ڈھانچے بنانے کے لیے متعدد پروسیسنگ مراحل سے گزرنا پڑتا ہے، جن کو قطعی طور پر انفرادی چپس (ڈیز) میں تقسیم کیا جانا چاہیے۔ اگر ڈائسنگ کے عمل کے دوران الائنمنٹ یا کٹنگ میں اہم غلطیاں ہوں تو سرکٹس کو نقصان پہنچ سکتا ہے جس سے چپ کی فعالیت اور قابل اعتمادی متاثر ہوتی ہے۔ لہذا، اعلی درستگی ڈائسنگ ٹیکنالوجی نہ صرف ہر چپ کی سالمیت کو یقینی بناتی ہے بلکہ اندرونی سرکٹس کو پہنچنے والے نقصان کو بھی روکتی ہے، مجموعی پیداوار کی شرح کو بہتر بناتی ہے۔
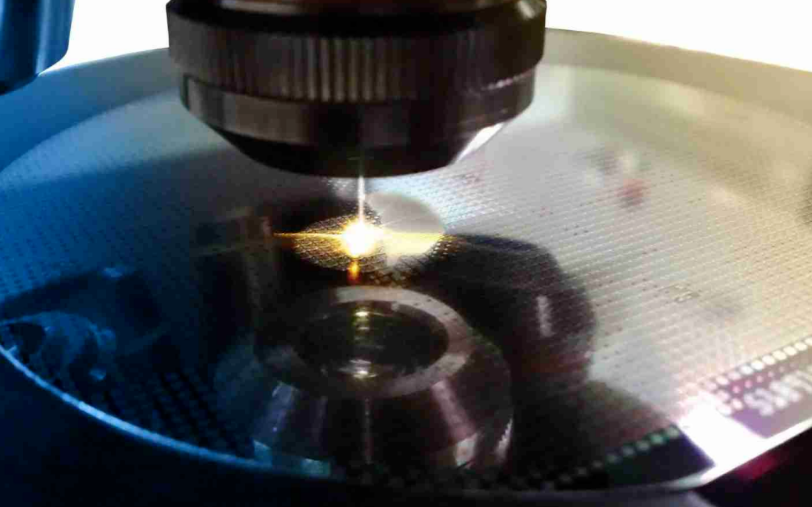
دوم، ویفر ڈائسنگ کا پیداواری کارکردگی اور لاگت کے کنٹرول پر نمایاں اثر پڑتا ہے۔ مینوفیکچرنگ کے عمل میں ایک اہم قدم کے طور پر، اس کی کارکردگی براہ راست بعد کے مراحل کی ترقی کو متاثر کرتی ہے۔ ڈائسنگ کے عمل کو بہتر بنا کر، آٹومیشن کی سطح کو بڑھا کر، اور کاٹنے کی رفتار کو بہتر بنا کر، مجموعی پیداوار کی کارکردگی کو بہت زیادہ بڑھایا جا سکتا ہے۔
دوسری طرف، ڈائسنگ کے دوران مواد کا ضیاع لاگت کے انتظام میں ایک اہم عنصر ہے۔ ڈائسنگ کی جدید ٹیکنالوجیز کا استعمال نہ صرف کاٹنے کے عمل کے دوران غیر ضروری مادی نقصانات کو کم کرتا ہے بلکہ ویفر کے استعمال میں بھی اضافہ کرتا ہے، اس طرح پیداواری لاگت کم ہوتی ہے۔
سیمی کنڈکٹر ٹکنالوجی میں ترقی کے ساتھ، ویفر کے قطر میں اضافہ ہوتا رہتا ہے، اور سرکٹ کی کثافت اسی کے مطابق بڑھتی ہے، جس سے ڈائسنگ ٹیکنالوجی پر زیادہ مطالبات ہوتے ہیں۔ بڑے ویفرز کو کاٹنے والے راستوں پر زیادہ درست کنٹرول کی ضرورت ہوتی ہے، خاص طور پر زیادہ کثافت والے سرکٹ والے علاقوں میں، جہاں معمولی انحراف بھی متعدد چپس کو خراب کر سکتا ہے۔ مزید برآں، بڑے ویفرز میں مزید کٹنگ لائنز اور زیادہ پیچیدہ عمل کے مراحل شامل ہوتے ہیں، ان چیلنجوں سے نمٹنے کے لیے ڈائسنگ ٹیکنالوجیز کی درستگی، مستقل مزاجی اور کارکردگی میں مزید بہتری کی ضرورت ہوتی ہے۔
1.3 ویفر ڈائسنگ کا عمل
ویفر ڈائسنگ کا عمل تیاری کے مرحلے سے لے کر حتمی معیار کے معائنے تک کے تمام مراحل پر محیط ہے، ہر مرحلہ ڈائس شدہ چپس کے معیار اور کارکردگی کو یقینی بنانے کے لیے اہم ہے۔ ذیل میں ہر مرحلے کی تفصیلی وضاحت ہے۔
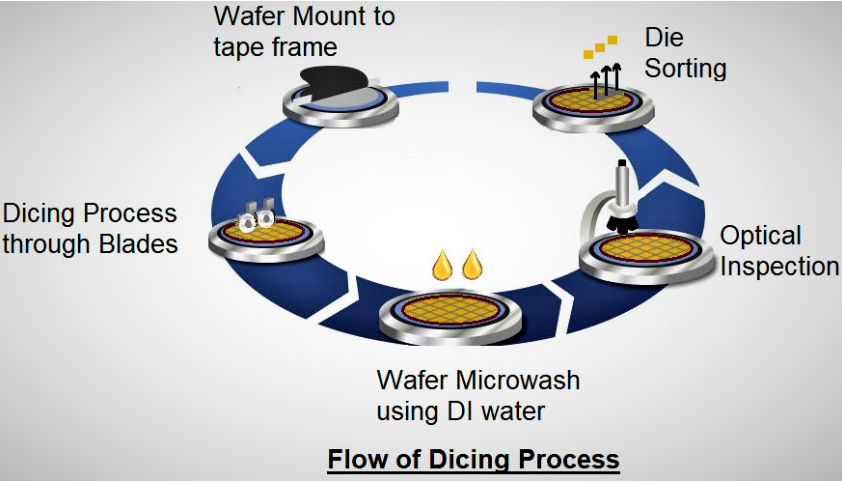
مرحلہ | تفصیلی تفصیل |
تیاری کا مرحلہ | -ویفر کی صفائی: نجاستوں، ذرات اور آلودگی کو دور کرنے کے لیے، الٹراسونک یا مکینیکل اسکربنگ کے ساتھ مل کر اعلیٰ پاکیزہ پانی اور صفائی کے خصوصی ایجنٹوں کا استعمال کریں، صاف سطح کو یقینی بنانے کے لیے۔ -عین مطابق پوزیشننگ: اس بات کو یقینی بنانے کے لیے کہ ویفر کو کٹنگ کے ڈیزائن کردہ راستوں پر درست طریقے سے تقسیم کیا گیا ہے، اعلیٰ درستگی والے آلات کا استعمال کریں۔ -ویفر فکسیشن: کاٹنے کے دوران استحکام کو برقرار رکھنے، کمپن یا حرکت سے ہونے والے نقصان کو روکنے کے لیے ویفر کو ٹیپ کے فریم پر محفوظ کریں۔ |
کٹنگ کا مرحلہ | -بلیڈ ڈائسنگ: فزیکل کٹنگ کے لیے تیز رفتار گھومنے والے ڈائمنڈ کوٹڈ بلیڈ استعمال کریں، جو سلیکون پر مبنی مواد کے لیے موزوں اور سستے ہوں۔ -لیزر ڈائسنگ: غیر رابطہ کاٹنے کے لیے ہائی انرجی لیزر بیم کا استعمال کریں، جو ٹوٹنے والے یا زیادہ سختی والے مواد جیسے گیلیم نائٹرائڈ کے لیے مثالی ہیں، زیادہ درستگی اور کم مواد کے نقصان کی پیشکش کرتے ہیں۔ -نئی ٹیکنالوجیز: گرمی سے متاثرہ علاقوں کو کم سے کم کرتے ہوئے کارکردگی اور درستگی کو مزید بہتر بنانے کے لیے لیزر اور پلازما کٹنگ ٹیکنالوجیز متعارف کروائیں۔ |
صفائی کا مرحلہ | - کاٹنے کے دوران پیدا ہونے والے ملبے اور دھول کو ہٹانے کے لیے، الٹراسونک یا اسپرے کی صفائی کے ساتھ مل کر ڈی آئنائزڈ واٹر (DI واٹر) اور خصوصی صفائی والے ایجنٹوں کا استعمال کریں، باقیات کو بعد کے عمل یا چپ برقی کارکردگی کو متاثر کرنے سے روکیں۔ - اعلی پاکیزگی والا DI پانی نئے آلودگیوں کو متعارف کرانے سے گریز کرتا ہے، صاف ویفر ماحول کو یقینی بناتا ہے۔ |
معائنہ کا مرحلہ | -آپٹیکل معائنہ: نقائص کی تیزی سے نشاندہی کرنے کے لیے AI الگورتھم کے ساتھ مل کر آپٹیکل ڈٹیکشن سسٹم کا استعمال کریں، اس بات کو یقینی بناتے ہوئے کہ ڈائس شدہ چپس میں کوئی دراڑ نہ پڑے، معائنہ کی کارکردگی کو بہتر بنایا جائے، اور انسانی غلطی کو کم کیا جائے۔ -طول و عرض کی پیمائش: تصدیق کریں کہ چپ کے طول و عرض ڈیزائن کی تصریحات پر پورا اترتے ہیں۔ -الیکٹریکل پرفارمنس ٹیسٹنگ: اس بات کو یقینی بنائیں کہ اہم چپس کی برقی کارکردگی معیارات پر پورا اترتی ہے، بعد میں آنے والی ایپلی کیشنز میں وشوسنییتا کی ضمانت دیتا ہے۔ |
چھانٹی کا مرحلہ | - کوالیفائیڈ چپس کو ٹیپ فریم سے الگ کرنے کے لیے روبوٹک بازو یا ویکیوم سکشن کپ کا استعمال کریں اور کارکردگی کی بنیاد پر خودکار طریقے سے ترتیب دیں، درستگی کو بہتر بناتے ہوئے پیداواری کارکردگی اور لچک کو یقینی بنائیں۔ |
ویفر کاٹنے کے عمل میں ویفر کی صفائی، پوزیشننگ، کٹنگ، صفائی، معائنہ اور چھانٹنا شامل ہوتا ہے، جس میں ہر قدم اہم ہوتا ہے۔ آٹومیشن، لیزر کٹنگ، اور اے آئی انسپکشن ٹیکنالوجیز میں ترقی کے ساتھ، جدید ویفر کٹنگ سسٹمز زیادہ درستگی، رفتار اور کم مواد کے نقصان کو حاصل کر سکتے ہیں۔ مستقبل میں، نئی کٹنگ ٹیکنالوجیز جیسے لیزر اور پلازما بتدریج روایتی بلیڈ کٹنگ کی جگہ لے لیں گے تاکہ تیزی سے پیچیدہ چپ ڈیزائن کی ضروریات کو پورا کیا جا سکے، اور سیمی کنڈکٹر مینوفیکچرنگ کے عمل کی ترقی کو آگے بڑھایا جا سکے۔
ویفر کٹنگ ٹیکنالوجی اور اس کے اصول
تصویر تین عام ویفر کاٹنے والی ٹیکنالوجیز کی وضاحت کرتی ہے:بلیڈ ڈائسنگ,لیزر ڈائسنگ، اورپلازما ڈائسنگ. ذیل میں ان تین تکنیکوں کا تفصیلی تجزیہ اور اضافی وضاحت دی گئی ہے۔
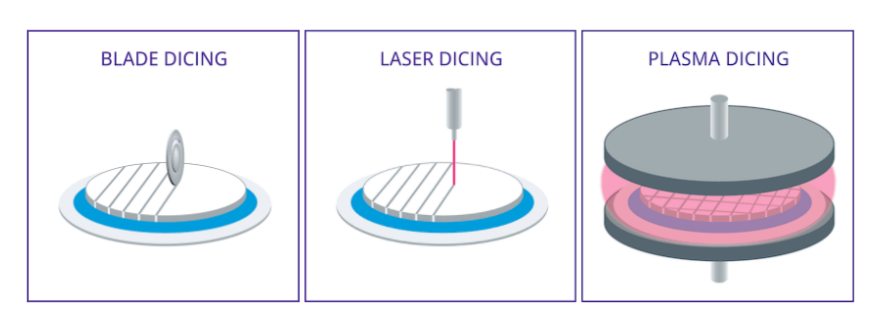
سیمی کنڈکٹر مینوفیکچرنگ میں، ویفر کی کٹنگ ایک اہم مرحلہ ہے جس کے لیے ویفر کی موٹائی کی بنیاد پر کاٹنے کا مناسب طریقہ منتخب کرنے کی ضرورت ہوتی ہے۔ پہلا قدم ویفر کی موٹائی کا تعین کرنا ہے۔ اگر ویفر کی موٹائی 100 مائکرون سے زیادہ ہے، تو بلیڈ ڈائسنگ کو کاٹنے کے طریقہ کے طور پر منتخب کیا جا سکتا ہے۔ اگر بلیڈ ڈائسنگ مناسب نہیں ہے تو، فریکچر ڈائسنگ کا طریقہ استعمال کیا جا سکتا ہے، جس میں سکریب کٹنگ اور بلیڈ ڈائسنگ کی تکنیک دونوں شامل ہیں۔
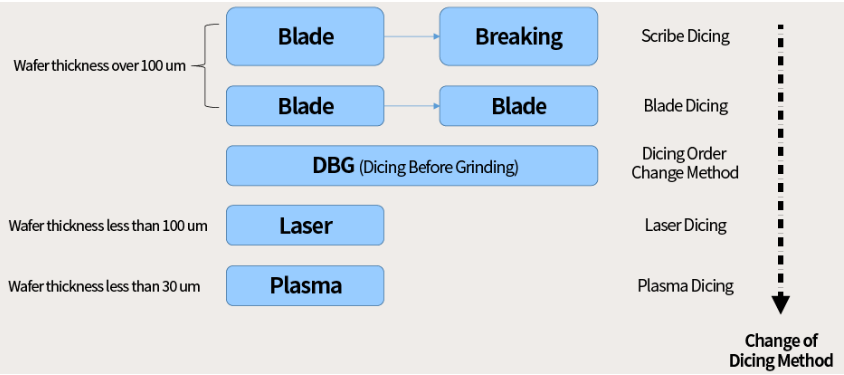
جب ویفر کی موٹائی 30 اور 100 مائیکرون کے درمیان ہو، تو DBG (پیسنے سے پہلے نرد) طریقہ تجویز کیا جاتا ہے۔ اس صورت میں، بہترین نتائج حاصل کرنے کے لیے سکریب کٹنگ، بلیڈ ڈائسنگ، یا ضرورت کے مطابق کٹنگ کی ترتیب کو ایڈجسٹ کرنے کا انتخاب کیا جا سکتا ہے۔
30 مائیکرون سے کم موٹائی والے انتہائی پتلے ویفرز کے لیے، لیزر کٹنگ ترجیحی طریقہ بن جاتا ہے کیونکہ اس کی صلاحیت کی وجہ سے پتلی ویفرز کو زیادہ نقصان پہنچائے بغیر درست طریقے سے کاٹنے کی صلاحیت ہے۔ اگر لیزر کٹنگ مخصوص ضروریات کو پورا نہیں کرسکتی ہے تو، پلازما کٹنگ کو متبادل کے طور پر استعمال کیا جاسکتا ہے۔ یہ فلو چارٹ فیصلہ سازی کا واضح راستہ فراہم کرتا ہے تاکہ یہ یقینی بنایا جا سکے کہ موٹائی کے مختلف حالات میں موزوں ترین ویفر کٹنگ ٹیکنالوجی کا انتخاب کیا گیا ہے۔
2.1 مکینیکل کٹنگ ٹیکنالوجی
مکینیکل کٹنگ ٹیکنالوجی ویفر ڈائسنگ میں روایتی طریقہ ہے۔ بنیادی اصول یہ ہے کہ تیز رفتار گھومنے والے ڈائمنڈ پیسنے والے پہیے کو کاٹنے کے آلے کے طور پر ویفر کو کاٹنا ہے۔ کلیدی سازوسامان میں ایئر بیئرنگ اسپنڈل شامل ہوتا ہے، جو ڈائمنڈ پیسنے والے پہیے کے آلے کو تیز رفتاری سے چلاتا ہے تاکہ پہلے سے طے شدہ کٹنگ کے راستے پر عین مطابق کٹائی یا نالی ہو سکے۔ اس ٹیکنالوجی کو اس کی کم قیمت، اعلی کارکردگی، اور وسیع اطلاق کی وجہ سے صنعت میں وسیع پیمانے پر استعمال کیا جاتا ہے۔
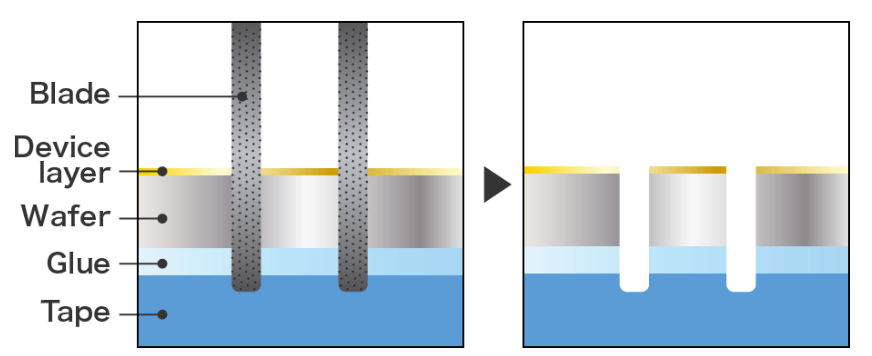
فوائد
ڈائمنڈ گرائنڈنگ وہیل ٹولز کی اعلی سختی اور پہننے کی مزاحمت مکینیکل کٹنگ ٹکنالوجی کو مختلف ویفر میٹریل کی کٹنگ ضروریات کے مطابق ڈھالنے کے قابل بناتی ہے، چاہے وہ روایتی سلکان پر مبنی مواد ہوں یا نئے کمپاؤنڈ سیمی کنڈکٹرز۔ اس کا آپریشن آسان ہے، نسبتاً کم تکنیکی ضروریات کے ساتھ، بڑے پیمانے پر پیداوار میں اس کی مقبولیت کو مزید فروغ دیتا ہے۔ مزید برآں، کاٹنے کے دیگر طریقوں جیسے لیزر کٹنگ کے مقابلے، مکینیکل کٹنگ میں زیادہ قابل کنٹرول لاگت ہوتی ہے، جو اسے اعلیٰ حجم کی پیداواری ضروریات کے لیے موزوں بناتی ہے۔
حدود
اس کے بے شمار فوائد کے باوجود، مکینیکل کٹنگ ٹیکنالوجی کی بھی حدود ہیں۔ سب سے پہلے، ٹول اور ویفر کے درمیان جسمانی رابطے کی وجہ سے، کاٹنے کی درستگی نسبتاً محدود ہے، جو اکثر جہتی انحراف کا باعث بنتی ہے جو بعد میں چپ کی پیکیجنگ اور جانچ کی درستگی کو متاثر کر سکتی ہے۔ دوم، مکینیکل کاٹنے کے عمل کے دوران چِپنگ اور کریکس جیسے نقائص آسانی سے پیدا ہو سکتے ہیں، جو نہ صرف پیداوار کی شرح کو متاثر کرتے ہیں بلکہ چپس کی وشوسنییتا اور عمر کو بھی منفی طور پر متاثر کر سکتے ہیں۔ مکینیکل تناؤ سے پیدا ہونے والا نقصان خاص طور پر اعلی کثافت چپ کی تیاری کے لیے نقصان دہ ہے، خاص طور پر جب ٹوٹنے والے مواد کو کاٹتے ہوئے، جہاں یہ مسائل زیادہ نمایاں ہوتے ہیں۔
تکنیکی بہتری
ان حدود پر قابو پانے کے لیے، محققین مکینیکل کاٹنے کے عمل کو مسلسل بہتر بنا رہے ہیں۔ کلیدی اصلاحات میں پیسنے والے پہیوں کے ڈیزائن اور مواد کے انتخاب کو بڑھانا شامل ہے تاکہ کاٹنے کی درستگی اور استحکام کو بہتر بنایا جا سکے۔ مزید برآں، کاٹنے کے سامان کے ساختی ڈیزائن اور کنٹرول سسٹم کو بہتر بنانے سے کاٹنے کے عمل کے استحکام اور آٹومیشن میں مزید بہتری آئی ہے۔ یہ پیشرفت انسانی کارروائیوں کی وجہ سے ہونے والی غلطیوں کو کم کرتی ہے اور کٹوتیوں کی مستقل مزاجی کو بہتر کرتی ہے۔ کاٹنے کے عمل کے دوران بے ضابطگیوں کی اصل وقتی نگرانی کے لیے جدید معائنہ اور کوالٹی کنٹرول ٹیکنالوجیز کے متعارف ہونے سے کاٹنے کے اعتبار اور پیداوار میں بھی نمایاں بہتری آئی ہے۔
مستقبل کی ترقی اور نئی ٹیکنالوجیز
اگرچہ مکینیکل کٹنگ ٹکنالوجی اب بھی ویفر کٹنگ میں ایک اہم مقام رکھتی ہے، سیمی کنڈکٹر کے عمل کے ارتقا کے ساتھ نئی کٹنگ ٹیکنالوجیز تیزی سے آگے بڑھ رہی ہیں۔ مثال کے طور پر، تھرمل لیزر کٹنگ ٹیکنالوجی کا اطلاق مکینیکل کٹنگ میں درستگی اور خرابی کے مسائل کے نئے حل فراہم کرتا ہے۔ یہ غیر رابطہ کاٹنے کا طریقہ ویفر پر جسمانی دباؤ کو کم کرتا ہے، خاص طور پر جب زیادہ ٹوٹنے والے مواد کو کاٹتا ہے تو چپکنے اور ٹوٹنے کے واقعات کو نمایاں طور پر کم کرتا ہے۔ مستقبل میں، ابھرتی ہوئی کٹنگ تکنیک کے ساتھ مکینیکل کٹنگ ٹیکنالوجی کا انضمام سیمی کنڈکٹر مینوفیکچرنگ کو مزید اختیارات اور لچک فراہم کرے گا، جس سے مینوفیکچرنگ کی کارکردگی اور چپ کے معیار میں مزید اضافہ ہوگا۔
آخر میں، اگرچہ مکینیکل کٹنگ ٹیکنالوجی میں کچھ خامیاں ہیں، مسلسل تکنیکی بہتری اور نئی کٹنگ تکنیکوں کے ساتھ اس کا انضمام اسے اب بھی سیمی کنڈکٹر مینوفیکچرنگ میں اہم کردار ادا کرنے اور مستقبل کے عمل میں اپنی مسابقت کو برقرار رکھنے کی اجازت دیتا ہے۔
2.2 لیزر کٹنگ ٹیکنالوجی
لیزر کٹنگ ٹیکنالوجی، ویفر کٹنگ میں ایک نئے طریقہ کے طور پر، سیمی کنڈکٹر کی صنعت میں اپنی اعلیٰ درستگی، مکینیکل رابطے کے نقصان کی کمی، اور تیزی سے کاٹنے کی صلاحیتوں کی وجہ سے آہستہ آہستہ وسیع پیمانے پر توجہ حاصل کر چکی ہے۔ یہ ٹیکنالوجی لیزر بیم کی اعلی توانائی کی کثافت اور توجہ مرکوز کرنے کی صلاحیت کا استعمال کرتی ہے تاکہ ویفر مواد کی سطح پر گرمی سے متاثرہ ایک چھوٹا سا زون بنایا جا سکے۔ جب لیزر بیم کو ویفر پر لگایا جاتا ہے، تو پیدا ہونے والا تھرمل تناؤ مواد کو مخصوص جگہ پر ٹوٹنے کا سبب بنتا ہے، جس سے قطعی کٹنگ ہوتی ہے۔
لیزر کٹنگ ٹیکنالوجی کے فوائد
• اعلی صحت سے متعلق: لیزر بیم کی درست پوزیشننگ کی صلاحیت مائیکرون یا حتیٰ کہ نینو میٹر سطح کی کٹنگ کی درستگی کی اجازت دیتی ہے، جو جدید اعلیٰ درستگی، اعلی کثافت مربوط سرکٹ مینوفیکچرنگ کی ضروریات کو پورا کرتی ہے۔
• کوئی مکینیکل رابطہ نہیں۔: لیزر کٹنگ ویفر کے ساتھ جسمانی رابطے سے گریز کرتی ہے، مکینیکل کٹنگ میں عام مسائل کو روکتی ہے، جیسے چِپنگ اور کریکنگ، نمایاں طور پر پیداوار کی شرح اور چپس کی وشوسنییتا کو بہتر بناتی ہے۔
• فاسٹ کاٹنے کی رفتار: لیزر کٹنگ کی تیز رفتار پیداوار کی کارکردگی میں اضافہ کرتی ہے، یہ خاص طور پر بڑے پیمانے پر، تیز رفتار پیداوار کے منظرناموں کے لیے موزوں ہے۔
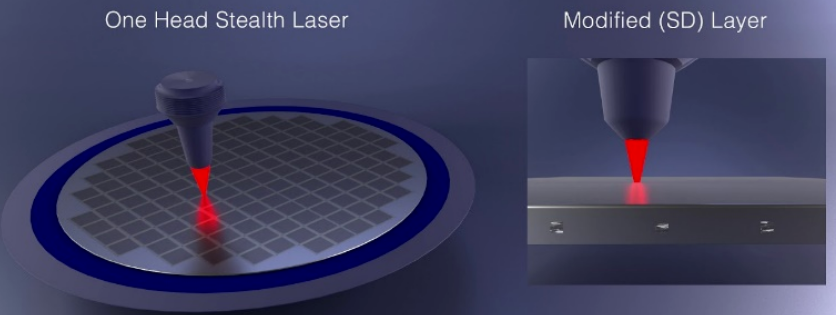
چیلنجز کا سامنا کرنا پڑا
• اعلی سازوسامان کی قیمت: لیزر کٹنگ آلات کے لیے ابتدائی سرمایہ کاری زیادہ ہے، جو معاشی دباؤ کو پیش کرتی ہے، خاص طور پر چھوٹے سے درمیانے درجے کے پیداواری اداروں کے لیے۔
• پیچیدہ عمل کا کنٹرول: لیزر کٹنگ کے لیے کئی پیرامیٹرز کے عین مطابق کنٹرول کی ضرورت ہوتی ہے، بشمول توانائی کی کثافت، فوکس پوزیشن، اور کاٹنے کی رفتار، جس سے عمل پیچیدہ ہوتا ہے۔
• گرمی سے متاثرہ زون کے مسائل: اگرچہ لیزر کٹنگ کی غیر رابطہ نوعیت مکینیکل نقصان کو کم کرتی ہے، تاہم گرمی سے متاثرہ زون (HAZ) کی وجہ سے تھرمل تناؤ ویفر مواد کی خصوصیات پر منفی اثر ڈال سکتا ہے۔ اس اثر کو کم کرنے کے لیے عمل کی مزید اصلاح کی ضرورت ہے۔
تکنیکی بہتری کی ہدایات
ان چیلنجوں سے نمٹنے کے لیے، محققین سامان کی لاگت کو کم کرنے، کارکردگی کو کم کرنے اور عمل کے بہاؤ کو بہتر بنانے پر توجہ دے رہے ہیں۔
• موثر لیزرز اور آپٹیکل سسٹمز: زیادہ موثر لیزرز اور جدید آپٹیکل سسٹم تیار کرنے سے، کاٹنے کی درستگی اور رفتار کو بڑھاتے ہوئے آلات کی لاگت کو کم کرنا ممکن ہے۔
• عمل کے پیرامیٹرز کو بہتر بنانا: لیزرز اور ویفر مواد کے درمیان تعامل کے بارے میں گہرائی سے تحقیق کی جا رہی ہے تاکہ عمل کو بہتر بنایا جا سکے جو گرمی سے متاثرہ زون کو کم کرتے ہیں، اس طرح کاٹنے کے معیار کو بہتر بناتے ہیں۔
• ذہین کنٹرول سسٹمز: ذہین کنٹرول ٹیکنالوجیز کی ترقی کا مقصد لیزر کاٹنے کے عمل کو خودکار اور بہتر بنانا، اس کے استحکام اور مستقل مزاجی کو بہتر بنانا ہے۔
لیزر کٹنگ ٹیکنالوجی انتہائی پتلی ویفرز اور اعلیٰ صحت سے متعلق کاٹنے کے منظرناموں میں خاص طور پر موثر ہے۔ جیسے جیسے ویفر کے سائز میں اضافہ ہوتا ہے اور سرکٹ کی کثافت میں اضافہ ہوتا ہے، روایتی مکینیکل کاٹنے کے طریقے جدید سیمی کنڈکٹر مینوفیکچرنگ کے اعلیٰ درستگی اور اعلیٰ کارکردگی کے تقاضوں کو پورا کرنے کے لیے جدوجہد کرتے ہیں۔ اس کے منفرد فوائد کی وجہ سے، لیزر کٹنگ ان شعبوں میں ترجیحی حل بن رہی ہے۔
اگرچہ لیزر کٹنگ ٹیکنالوجی کو اب بھی چیلنجز کا سامنا ہے جیسے کہ اعلی سازوسامان کی لاگت اور عمل کی پیچیدگی، اعلیٰ درستگی اور غیر رابطہ نقصان میں اس کے منفرد فوائد اسے سیمی کنڈکٹر مینوفیکچرنگ میں ترقی کے لیے ایک اہم سمت بناتے ہیں۔ جیسا کہ لیزر ٹیکنالوجی اور ذہین کنٹرول سسٹم آگے بڑھ رہے ہیں، توقع ہے کہ لیزر کٹنگ سے ویفر کٹنگ کی کارکردگی اور معیار میں مزید بہتری آئے گی، جس سے سیمی کنڈکٹر انڈسٹری کی مسلسل ترقی ہوگی۔
2.3 پلازما کٹنگ ٹیکنالوجی
پلازما کٹنگ ٹیکنالوجی، ایک ابھرتے ہوئے ویفر ڈائسنگ طریقہ کے طور پر، حالیہ برسوں میں خاصی توجہ حاصل کر چکی ہے۔ یہ ٹکنالوجی پلازما بیم کی توانائی، رفتار، اور کٹنگ پاتھ کو کنٹرول کرکے ویفرز کو درست طریقے سے کاٹنے کے لیے ہائی انرجی پلازما بیم کا استعمال کرتی ہے، کاٹنے کے بہترین نتائج حاصل کرتے ہیں۔
کام کرنے کا اصول اور فوائد
پلازما کاٹنے کا عمل آلات کے ذریعے پیدا ہونے والے اعلی درجہ حرارت، اعلی توانائی والے پلازما بیم پر انحصار کرتا ہے۔ یہ شہتیر ویفر مواد کو بہت کم وقت میں اس کے پگھلنے یا بخارات کے نقطہ پر گرم کر سکتا ہے، جس سے تیزی سے کٹائی ممکن ہو سکتی ہے۔ روایتی مکینیکل یا لیزر کٹنگ کے مقابلے میں، پلازما کی کٹنگ تیز ہوتی ہے اور گرمی سے متاثرہ ایک چھوٹا زون پیدا کرتی ہے، جو کاٹنے کے دوران دراڑیں اور نقصان کو مؤثر طریقے سے کم کرتی ہے۔
عملی ایپلی کیشنز میں، پلازما کٹنگ ٹیکنالوجی خاص طور پر پیچیدہ شکلوں والے ویفرز کو سنبھالنے میں ماہر ہے۔ اس کی اعلی توانائی، سایڈست پلازما بیم آسانی سے بے ترتیب شکل والے ویفرز کو اعلیٰ درستگی کے ساتھ کاٹ سکتی ہے۔ لہٰذا، مائیکرو الیکٹرانکس مینوفیکچرنگ میں، خاص طور پر اعلیٰ درجے کے چپس کی اپنی مرضی کے مطابق اور چھوٹے بیچ کی پیداوار میں، یہ ٹیکنالوجی وسیع پیمانے پر استعمال کے لیے بہترین وعدہ ظاہر کرتی ہے۔
چیلنجز اور حدود
پلازما کٹنگ ٹیکنالوجی کے بہت سے فوائد کے باوجود اسے کچھ چیلنجز کا بھی سامنا ہے۔
• پیچیدہ عمل: پلازما کاٹنے کا عمل پیچیدہ ہے اور اس کو یقینی بنانے کے لیے اعلیٰ درستگی کے آلات اور تجربہ کار آپریٹرز کی ضرورت ہوتی ہے۔کاٹنے میں درستگی اور استحکام۔
• ماحولیاتی کنٹرول اور حفاظت: پلازما بیم کی اعلی درجہ حرارت، اعلی توانائی کی نوعیت کے لیے سخت ماحولیاتی کنٹرول اور حفاظتی اقدامات کی ضرورت ہوتی ہے، جس سے عمل درآمد کی پیچیدگی اور لاگت میں اضافہ ہوتا ہے۔
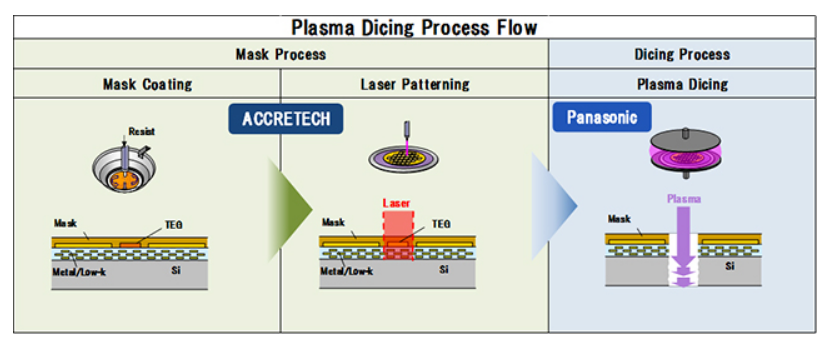
مستقبل کی ترقی کی سمت
تکنیکی ترقی کے ساتھ، پلازما کاٹنے سے وابستہ چیلنجوں پر بتدریج قابو پانے کی امید ہے۔ زیادہ ہوشیار اور زیادہ مستحکم کاٹنے کے آلات تیار کرکے، دستی آپریشنز پر انحصار کو کم کیا جا سکتا ہے، اس طرح پیداوار کی کارکردگی کو بہتر بنایا جا سکتا ہے۔ ایک ہی وقت میں، عمل کے پیرامیٹرز اور کاٹنے والے ماحول کو بہتر بنانے سے حفاظتی خطرات اور آپریشنل اخراجات کو کم کرنے میں مدد ملے گی۔
سیمی کنڈکٹر انڈسٹری میں، ویفر کٹنگ اور ڈائسنگ ٹیکنالوجی میں اختراعات صنعت کی ترقی کو آگے بڑھانے کے لیے اہم ہیں۔ پلازما کٹنگ ٹیکنالوجی، اپنی اعلیٰ درستگی، کارکردگی، اور پیچیدہ ویفر کی شکلوں کو سنبھالنے کی صلاحیت کے ساتھ، اس میدان میں ایک اہم نئے کھلاڑی کے طور پر ابھری ہے۔ اگرچہ کچھ چیلنجز باقی ہیں، ان مسائل کو بتدریج مسلسل تکنیکی جدت طرازی کے ساتھ حل کیا جائے گا، جس سے سیمی کنڈکٹر مینوفیکچرنگ میں مزید امکانات اور مواقع پیدا ہوں گے۔
پلازما کٹنگ ٹیکنالوجی کے استعمال کے امکانات بہت وسیع ہیں، اور امید کی جاتی ہے کہ یہ مستقبل میں سیمی کنڈکٹر مینوفیکچرنگ میں زیادہ اہم کردار ادا کرے گی۔ مسلسل تکنیکی جدت طرازی اور اصلاح کے ذریعے، پلازما کٹنگ نہ صرف موجودہ چیلنجوں سے نمٹائے گی بلکہ سیمی کنڈکٹر انڈسٹری کی ترقی کا ایک طاقتور ڈرائیور بھی بن جائے گی۔
2.4 معیار کو کم کرنا اور عوامل کو متاثر کرنا
بعد میں آنے والی چپ پیکیجنگ، ٹیسٹنگ، اور حتمی مصنوعات کی مجموعی کارکردگی اور وشوسنییتا کے لیے ویفر کٹنگ کا معیار اہم ہے۔ کاٹنے کے دوران جن عام مسائل کا سامنا کرنا پڑتا ہے ان میں دراڑیں، چٹائی اور کٹائی انحراف شامل ہیں۔ یہ مسائل مل کر کام کرنے والے کئی عوامل سے متاثر ہوتے ہیں۔
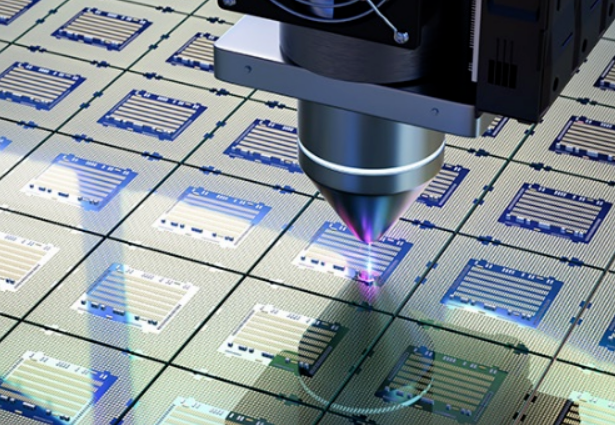
زمرہ | مواد | اثر |
عمل کے پیرامیٹرز | کاٹنے کی رفتار، فیڈ کی شرح، اور کاٹنے کی گہرائی براہ راست کاٹنے کے عمل کے استحکام اور درستگی کو متاثر کرتی ہے۔ غلط سیٹنگز تناؤ کے ارتکاز اور ضرورت سے زیادہ گرمی سے متاثرہ زون کا باعث بن سکتی ہیں، جس کے نتیجے میں دراڑیں پڑتی ہیں اور چپکنا پڑتا ہے۔ ویفر مواد، موٹائی، اور کاٹنے کی ضروریات کی بنیاد پر پیرامیٹرز کو مناسب طریقے سے ایڈجسٹ کرنا مطلوبہ کاٹنے کے نتائج حاصل کرنے کی کلید ہے۔ | درست عمل کے پیرامیٹرز قطعی کٹنگ کو یقینی بناتے ہیں اور دراڑیں اور چپکنے جیسے نقائص کے خطرے کو کم کرتے ہیں۔ |
آلات اور مواد کے عوامل | -بلیڈ کوالٹی: بلیڈ کا مواد، سختی اور پہننے کی مزاحمت کاٹنے کے عمل کی ہمواری اور کٹی ہوئی سطح کی ہمواری کو متاثر کرتی ہے۔ ناقص معیار کے بلیڈ رگڑ اور تھرمل تناؤ کو بڑھاتے ہیں، جو ممکنہ طور پر دراڑیں یا چپکنے کا باعث بنتے ہیں۔ صحیح بلیڈ مواد کا انتخاب اہم ہے. -کولنٹ کی کارکردگی: کولنٹ درجہ حرارت کو کم کرنے، رگڑ کو کم کرنے اور ملبے کو صاف کرنے میں مدد کرتے ہیں۔ غیر موثر کولنٹ اعلی درجہ حرارت اور ملبے کے جمع ہونے کا باعث بن سکتا ہے، جس سے کاٹنے کے معیار اور کارکردگی متاثر ہوتی ہے۔ موثر اور ماحول دوست کولنٹس کا انتخاب بہت ضروری ہے۔ | بلیڈ کا معیار کٹ کی درستگی اور نرمی کو متاثر کرتا ہے۔ غیر موثر کولنٹ کا نتیجہ خراب کاٹنے کے معیار اور کارکردگی کا سبب بن سکتا ہے، جو کولنٹ کے بہترین استعمال کی ضرورت کو اجاگر کرتا ہے۔ |
پروسیس کنٹرول اور کوالٹی انسپیکشن | -عمل کا کنٹرول: کاٹنے کے عمل میں استحکام اور مستقل مزاجی کو یقینی بنانے کے لیے کلیدی کٹنگ پیرامیٹرز کی ریئل ٹائم نگرانی اور ایڈجسٹمنٹ۔ -معیار کا معائنہ: کاٹنے کے بعد ظاہری شکل کی جانچ پڑتال، جہتی پیمائش، اور برقی کارکردگی کی جانچ معیار کے مسائل کی فوری شناخت اور حل کرنے میں مدد کرتی ہے، جس سے کاٹنے کی درستگی اور مستقل مزاجی بہتر ہوتی ہے۔ | مناسب پراسیس کنٹرول اور کوالٹی انسپیکشن مسلسل، اعلیٰ معیار کے کٹنگ کے نتائج اور ممکنہ مسائل کا جلد پتہ لگانے میں مدد کرتا ہے۔ |

کاٹنے کے معیار کو بہتر بنانا
کاٹنے کے معیار کو بہتر بنانے کے لیے ایک جامع نقطہ نظر کی ضرورت ہوتی ہے جس میں عمل کے پیرامیٹرز، آلات اور مواد کے انتخاب، عمل کے کنٹرول اور معائنہ کو مدنظر رکھا جائے۔ کٹنگ ٹیکنالوجیز کو مسلسل بہتر بنانے اور عمل کے طریقوں کو بہتر بنانے سے، ویفر کٹنگ کی درستگی اور استحکام کو مزید بڑھایا جا سکتا ہے، جو سیمی کنڈکٹر مینوفیکچرنگ انڈسٹری کے لیے زیادہ قابل اعتماد تکنیکی مدد فراہم کرتا ہے۔
#03 پوسٹ کٹنگ ہینڈلنگ اور ٹیسٹنگ
3.1 صفائی اور خشک کرنا
ویفر کٹنگ کے بعد صفائی اور خشک کرنے کے اقدامات چپ کے معیار کو یقینی بنانے اور بعد کے عمل کی ہموار ترقی کے لیے اہم ہیں۔ اس مرحلے کے دوران، سلکان کے ملبے، کولنٹ کی باقیات، اور کاٹنے کے دوران پیدا ہونے والے دیگر آلودگیوں کو اچھی طرح سے ہٹانا ضروری ہے۔ یہ یقینی بنانا بھی اتنا ہی ضروری ہے کہ صفائی کے عمل کے دوران چپس کو نقصان نہ پہنچے، اور خشک ہونے کے بعد، اس بات کو یقینی بنائیں کہ چپ کی سطح پر کوئی نمی باقی نہ رہے تاکہ سنکنرن یا الیکٹرو سٹیٹک ڈسچارج جیسے مسائل کو روکا جا سکے۔
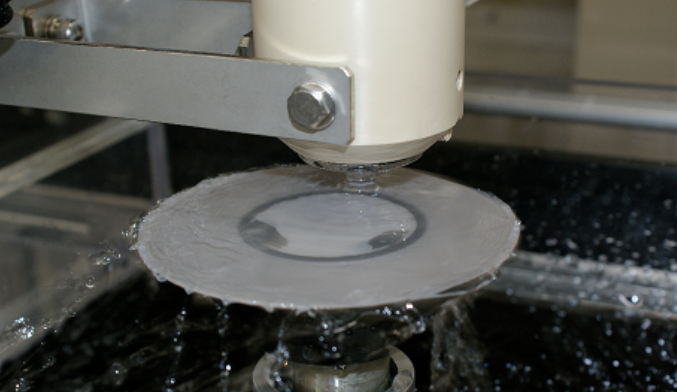
پوسٹ کٹنگ ہینڈلنگ: صفائی اور خشک کرنے کا عمل
عمل کا مرحلہ | مواد | اثر |
صفائی کا عمل | -طریقہ: صفائی کے لیے الٹراسونک یا مکینیکل برش کی تکنیکوں کے ساتھ مل کر صفائی کے خصوصی ایجنٹس اور خالص پانی کا استعمال کریں۔ | آلودگی کے مکمل خاتمے کو یقینی بناتا ہے اور صفائی کے دوران چپس کو پہنچنے والے نقصان کو روکتا ہے۔ |
-صفائی ایجنٹ کا انتخاب: چپ کو نقصان پہنچائے بغیر موثر صفائی کو یقینی بنانے کے لیے ویفر مواد اور آلودگی کی قسم کی بنیاد پر انتخاب کریں۔ | مؤثر صفائی اور چپ کے تحفظ کے لیے ایجنٹ کا مناسب انتخاب کلیدی حیثیت رکھتا ہے۔ | |
-پیرامیٹر کنٹرول: صفائی کے درجہ حرارت، وقت، اور صفائی کے حل کے ارتکاز کو سختی سے کنٹرول کریں تاکہ غلط صفائی کی وجہ سے معیار کے مسائل کو روکا جا سکے۔ | کنٹرولز ویفر کو نقصان پہنچانے یا آلودگیوں کو پیچھے چھوڑنے سے بچنے میں مدد کرتے ہیں، مستقل معیار کو یقینی بناتے ہیں۔ | |
خشک کرنے کا عمل | -روایتی طریقے: قدرتی ہوا خشک کرنا اور گرم ہوا خشک کرنا، جس کی کارکردگی کم ہے اور یہ جامد بجلی کی تعمیر کا باعث بن سکتی ہے۔ | اس کے نتیجے میں خشک ہونے کے اوقات اور ممکنہ جامد مسائل پیدا ہو سکتے ہیں۔ |
-جدید ٹیکنالوجیز: ویکیوم ڈرائینگ اور انفراریڈ ڈرائینگ جیسی جدید ٹیکنالوجیز استعمال کریں تاکہ چپس جلد سوکھیں اور نقصان دہ اثرات سے بچ سکیں۔ | تیز اور زیادہ موثر خشک کرنے کا عمل، جامد خارج ہونے والے مادہ یا نمی سے متعلق مسائل کے خطرے کو کم کرتا ہے۔ | |
سامان کا انتخاب اور دیکھ بھال | -سامان کا انتخاب: اعلی کارکردگی کی صفائی اور خشک کرنے والی مشینیں پروسیسنگ کی کارکردگی کو بہتر کرتی ہیں اور ہینڈلنگ کے دوران ممکنہ مسائل کو باریک کنٹرول کرتی ہیں۔ | اعلی معیار کی مشینیں بہتر پروسیسنگ کو یقینی بناتی ہیں اور صفائی اور خشک کرنے کے دوران غلطیوں کے امکانات کو کم کرتی ہیں۔ |
-سامان کی بحالی: سامان کا باقاعدہ معائنہ اور دیکھ بھال اس بات کو یقینی بناتی ہے کہ یہ بہترین کام کرنے کی حالت میں ہے، چپ کے معیار کی ضمانت دیتا ہے۔ | مناسب دیکھ بھال سامان کی ناکامی کو روکتی ہے، قابل اعتماد اور اعلیٰ معیار کی پروسیسنگ کو یقینی بناتی ہے۔ |
کاٹنے کے بعد کی صفائی اور خشک کرنا
ویفر کٹنگ کے بعد صفائی اور خشک کرنے کے مراحل پیچیدہ اور نازک عمل ہیں جن کے لیے حتمی پروسیسنگ کے نتائج کو یقینی بنانے کے لیے متعدد عوامل پر غور کرنے کی ضرورت ہوتی ہے۔ سائنسی طریقوں اور سخت طریقہ کار کو استعمال کرتے ہوئے، یہ یقینی بنانا ممکن ہے کہ ہر چپ بہترین حالت میں پیکیجنگ اور جانچ کے مراحل میں داخل ہو۔
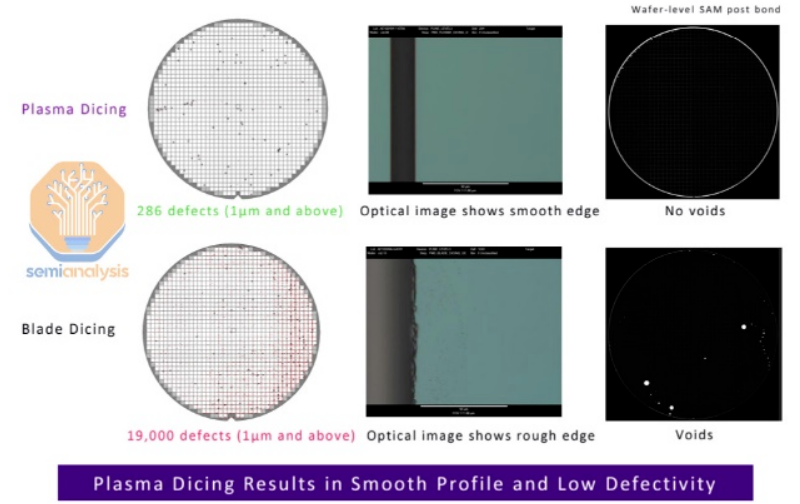
کاٹنے کے بعد معائنہ اور جانچ
قدم | مواد | اثر |
معائنہ کا مرحلہ | 1۔بصری معائنہ: بصری یا خودکار معائنہ کا سامان استعمال کریں تاکہ چپ کی سطح پر نظر آنے والے نقائص جیسے دراڑیں، چپکنا، یا آلودگی کی جانچ کریں۔ فضلہ سے بچنے کے لیے جسمانی طور پر خراب شدہ چپس کی فوری شناخت کریں۔ | مادی نقصان کو کم کرتے ہوئے، عمل کے شروع میں عیب دار چپس کی شناخت اور اسے ختم کرنے میں مدد کرتا ہے۔ |
2.سائز کی پیمائش: چپ کے طول و عرض کی درست پیمائش کرنے کے لیے درست پیمائش کرنے والے آلات کا استعمال کریں، اس بات کو یقینی بناتے ہوئے کہ کٹ سائز ڈیزائن کی وضاحتوں پر پورا اترتا ہے اور کارکردگی کے مسائل یا پیکیجنگ کی مشکلات کو روکتا ہے۔ | اس بات کو یقینی بناتا ہے کہ چپس مطلوبہ سائز کی حد کے اندر ہوں، کارکردگی میں کمی یا اسمبلی کے مسائل کو روکتی ہیں۔ | |
3.الیکٹریکل پرفارمنس ٹیسٹنگ: کلیدی برقی پیرامیٹرز کا اندازہ کریں جیسے کہ مزاحمت، اہلیت، اور انڈکٹنس، غیر موافق چپس کی شناخت کے لیے اور یقینی بنائیں کہ صرف کارکردگی کے لیے اہل چپس ہی اگلے مرحلے پر جائیں۔ | اس بات کو یقینی بناتا ہے کہ صرف فعال اور کارکردگی کی جانچ شدہ چپس ہی عمل میں آگے بڑھیں، جو بعد کے مراحل میں ناکامی کے خطرے کو کم کرتی ہیں۔ | |
ٹیسٹنگ مرحلہ | 1۔فنکشنل ٹیسٹنگ: توثیق کریں کہ چپ کی بنیادی فعالیت حسب منشا کام کرتی ہے، فنکشنل اسامانیتاوں کے ساتھ چپس کی شناخت اور اسے ختم کرتی ہے۔ | اس بات کو یقینی بناتا ہے کہ چپس بعد کے مراحل میں جانے سے پہلے بنیادی آپریشنل ضروریات کو پورا کرتی ہیں۔ |
2.وشوسنییتا کی جانچ: طویل استعمال یا سخت ماحول کے تحت چپ کی کارکردگی کے استحکام کا اندازہ کریں، جس میں عام طور پر اعلی درجہ حرارت کی عمر، کم درجہ حرارت کی جانچ، اور نمی کی جانچ شامل ہوتی ہے تاکہ حقیقی دنیا کے انتہائی حالات کی تقلید کی جا سکے۔ | اس بات کو یقینی بناتا ہے کہ چپس مختلف ماحولیاتی حالات میں قابل اعتماد طریقے سے کام کر سکتی ہیں، مصنوعات کی لمبی عمر اور استحکام کو بہتر بناتی ہیں۔ | |
3.مطابقت کی جانچ: اس بات کی تصدیق کریں کہ چپ دوسرے اجزاء یا سسٹمز کے ساتھ صحیح طریقے سے کام کرتی ہے، اس بات کو یقینی بناتے ہوئے کہ عدم مطابقت کی وجہ سے اس میں کوئی خرابی یا کارکردگی میں کمی نہیں ہے۔ | مطابقت کے مسائل کو روک کر حقیقی دنیا کی ایپلی کیشنز میں ہموار آپریشن کو یقینی بناتا ہے۔ |
3.3 پیکجنگ اور اسٹوریج
ویفر کاٹنے کے بعد، چپس سیمی کنڈکٹر مینوفیکچرنگ کے عمل کی ایک اہم پیداوار ہیں، اور ان کی پیکیجنگ اور اسٹوریج کے مراحل بھی اتنے ہی اہم ہیں۔ مناسب پیکیجنگ اور ذخیرہ کرنے کے اقدامات نہ صرف نقل و حمل اور اسٹوریج کے دوران چپس کی حفاظت اور استحکام کو یقینی بنانے کے لیے ضروری ہیں بلکہ اس کے بعد کی پیداوار، جانچ اور پیکیجنگ کے مراحل کے لیے مضبوط تعاون فراہم کرنے کے لیے بھی ضروری ہیں۔
معائنہ اور جانچ کے مراحل کا خلاصہ:
ویفر کٹنگ کے بعد چپس کے معائنے اور جانچ کے اقدامات مختلف پہلوؤں کا احاطہ کرتے ہیں، بشمول بصری معائنہ، سائز کی پیمائش، برقی کارکردگی کی جانچ، فنکشنل ٹیسٹنگ، وشوسنییتا کی جانچ، اور مطابقت کی جانچ۔ یہ اقدامات ایک دوسرے سے جڑے ہوئے اور تکمیلی ہیں، جو مصنوعات کے معیار اور وشوسنییتا کو یقینی بنانے کے لیے ایک ٹھوس رکاوٹ بناتے ہیں۔ سخت معائنہ اور جانچ کے طریقہ کار کے ذریعے، ممکنہ مسائل کی نشاندہی کی جا سکتی ہے اور اسے فوری طور پر حل کیا جا سکتا ہے، اس بات کو یقینی بناتے ہوئے کہ حتمی پروڈکٹ کسٹمر کی ضروریات اور توقعات پر پورا اترتی ہے۔
پہلو | مواد |
پیکجنگ کے اقدامات | 1۔مخالف جامد: پیکجنگ مواد میں بہترین اینٹی سٹیٹک خصوصیات ہونی چاہئیں تاکہ جامد بجلی کو آلات کو نقصان پہنچانے یا ان کی کارکردگی کو متاثر کرنے سے روک سکے۔ |
2.نمی پروف: پیکیجنگ مواد میں نمی کی اچھی مزاحمت ہونی چاہیے تاکہ نمی کی وجہ سے بجلی کی کارکردگی کو سنکنرن اور خراب ہونے سے بچایا جا سکے۔ | |
3.شاک پروف: پیکیجنگ مواد کو نقل و حمل کے دوران چپس کو کمپن اور اثرات سے بچانے کے لیے مؤثر جھٹکا جذب کرنا چاہیے۔ | |
ذخیرہ کرنے کا ماحول | 1۔نمی کنٹرول: ضرورت سے زیادہ نمی یا کم نمی کی وجہ سے جامد مسائل کی وجہ سے نمی جذب اور سنکنرن کو روکنے کے لیے مناسب حد کے اندر نمی کو سختی سے کنٹرول کریں۔ |
2.صفائی: دھول اور نجاست سے چپس کی آلودگی سے بچنے کے لیے ذخیرہ کرنے کے صاف ماحول کو برقرار رکھیں۔ | |
3.درجہ حرارت کنٹرول: درجہ حرارت کی ایک معقول حد مقرر کریں اور درجہ حرارت کے استحکام کو برقرار رکھیں تاکہ کم درجہ حرارت کی وجہ سے زیادہ گرمی یا گاڑھا ہونے کے مسائل کی وجہ سے تیز عمر بڑھنے سے بچ سکے۔ | |
باقاعدہ معائنہ | بصری معائنہ، سائز کی پیمائش، اور بروقت ممکنہ مسائل کی نشاندہی اور ان سے نمٹنے کے لیے برقی کارکردگی کے ٹیسٹ کا استعمال کرتے ہوئے ذخیرہ شدہ چپس کا باقاعدگی سے معائنہ اور جائزہ لیں۔ ذخیرہ کرنے کے وقت اور حالات کی بنیاد پر، چپس کے استعمال کا منصوبہ بنائیں تاکہ یہ یقینی بنایا جا سکے کہ وہ بہترین حالت میں استعمال ہوں۔ |
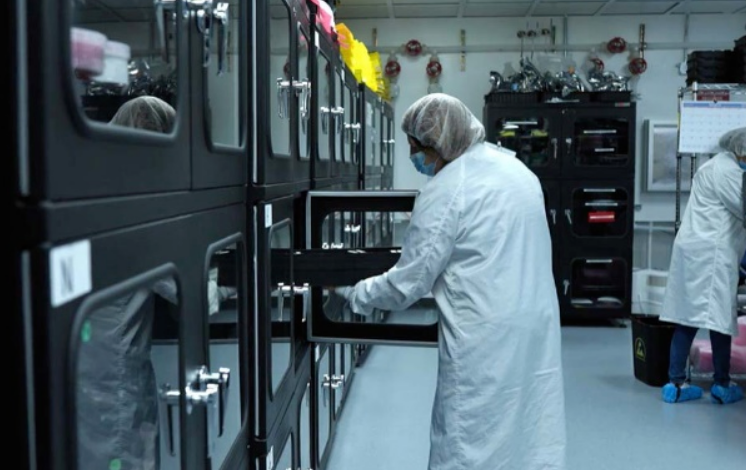
ویفر ڈائسنگ کے عمل کے دوران مائکرو کریکس اور نقصان کا مسئلہ سیمی کنڈکٹر مینوفیکچرنگ میں ایک اہم چیلنج ہے۔ کاٹنے کا تناؤ اس رجحان کی بنیادی وجہ ہے، کیونکہ یہ ویفر کی سطح پر چھوٹی دراڑیں اور نقصانات پیدا کرتا ہے، جس سے مینوفیکچرنگ لاگت میں اضافہ اور مصنوعات کے معیار میں کمی واقع ہوتی ہے۔
اس چیلنج سے نمٹنے کے لیے، کٹنگ تناؤ کو کم سے کم کرنا اور کاٹنے کی بہترین تکنیکوں، اوزاروں اور شرائط کو نافذ کرنا بہت ضروری ہے۔ بلیڈ مواد، کاٹنے کی رفتار، دباؤ، اور ٹھنڈک کے طریقوں جیسے عوامل پر احتیاط سے توجہ مائکرو کریکس کی تشکیل کو کم کرنے اور عمل کی مجموعی پیداوار کو بہتر بنانے میں مدد کر سکتی ہے۔ مزید برآں، مزید جدید کٹنگ ٹیکنالوجیز، جیسے لیزر ڈائسنگ، میں جاری تحقیق ان مسائل کو مزید کم کرنے کے طریقے تلاش کر رہی ہے۔
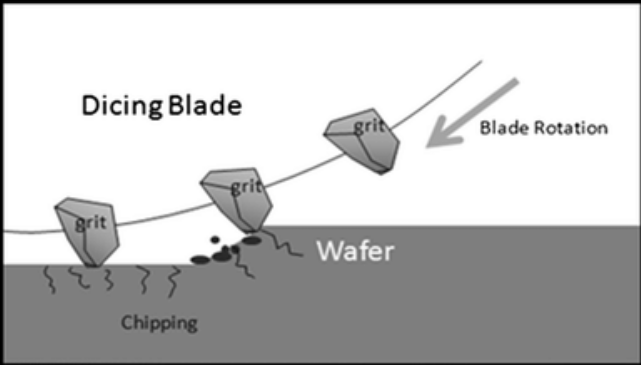
ایک نازک مواد کے طور پر، جب میکانی، تھرمل، یا کیمیائی تناؤ کا نشانہ بنایا جاتا ہے تو ویفرز اندرونی ساختی تبدیلیوں کا شکار ہوتے ہیں، جو مائیکرو کریکس کی تشکیل کا باعث بنتے ہیں۔ اگرچہ یہ دراڑیں فوری طور پر قابل توجہ نہیں ہوسکتی ہیں، لیکن مینوفیکچرنگ کے عمل کے آگے بڑھنے کے ساتھ یہ پھیل سکتے ہیں اور مزید شدید نقصان پہنچا سکتے ہیں۔ یہ مسئلہ بعد میں پیکیجنگ اور جانچ کے مراحل کے دوران خاص طور پر پریشانی کا باعث بنتا ہے، جہاں درجہ حرارت میں اتار چڑھاو اور اضافی میکانی دباؤ ان مائیکرو کریکس کو مرئی فریکچر میں تبدیل کرنے کا سبب بن سکتا ہے، جو ممکنہ طور پر چپ کی ناکامی کا باعث بنتا ہے۔
اس خطرے کو کم کرنے کے لیے، کاٹنے کی رفتار، دباؤ اور درجہ حرارت جیسے پیرامیٹرز کو بہتر بنا کر کاٹنے کے عمل کو احتیاط سے کنٹرول کرنا ضروری ہے۔ کم جارحانہ کاٹنے کے طریقوں کا استعمال، جیسے لیزر ڈائسنگ، ویفر پر مکینیکل دباؤ کو کم کر سکتا ہے اور مائکرو کریکس کی تشکیل کو کم کر سکتا ہے۔ مزید برآں، ویفر ڈائسنگ کے عمل کے دوران انفراریڈ اسکیننگ یا ایکس رے امیجنگ جیسے جدید معائنے کے طریقوں کو نافذ کرنے سے ان ابتدائی مرحلے کے دراڑوں کو مزید نقصان پہنچنے سے پہلے ان کا پتہ لگانے میں مدد مل سکتی ہے۔
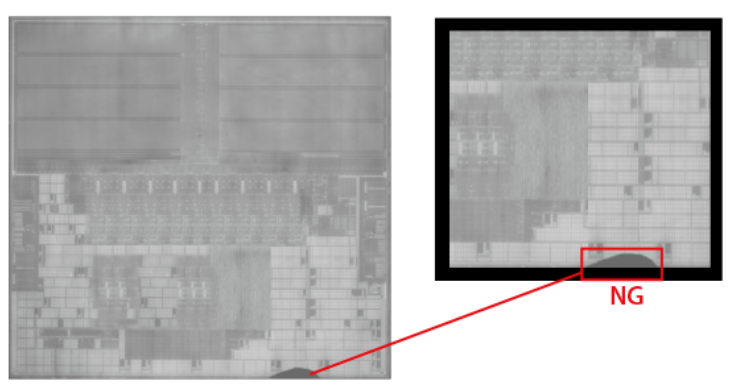
ڈائسنگ کے عمل میں ویفر کی سطح کو پہنچنے والا نقصان ایک اہم تشویش ہے، کیونکہ اس کا براہ راست اثر چپ کی کارکردگی اور وشوسنییتا پر پڑ سکتا ہے۔ اس طرح کا نقصان کاٹنے کے اوزار کے غلط استعمال، کاٹنے کے غلط پیرامیٹرز، یا خود ویفر میں موجود مادی نقائص کی وجہ سے ہو سکتا ہے۔ وجہ سے قطع نظر، یہ نقصانات سرکٹ کی برقی مزاحمت یا اہلیت میں تبدیلی کا باعث بن سکتے ہیں، جس سے مجموعی کارکردگی متاثر ہوتی ہے۔
ان مسائل کو حل کرنے کے لیے، دو اہم حکمت عملیوں کو تلاش کیا جا رہا ہے:
1. کاٹنے کے اوزار اور پیرامیٹرز کو بہتر بنانا: تیز بلیڈ استعمال کرکے، کاٹنے کی رفتار کو ایڈجسٹ کرکے، اور کاٹنے کی گہرائی میں ترمیم کرکے، کاٹنے کے عمل کے دوران تناؤ کے ارتکاز کو کم کیا جاسکتا ہے، اس طرح نقصان کے امکانات کو کم کیا جاسکتا ہے۔
2. نئی کاٹنے والی ٹیکنالوجیز کی تلاش: لیزر کٹنگ اور پلازما کٹنگ جیسی جدید تکنیکیں بہتر درستگی پیش کرتی ہیں جبکہ ممکنہ طور پر ویفر کو پہنچنے والے نقصان کی سطح کو کم کرتی ہیں۔ ویفر پر تھرمل اور مکینیکل دباؤ کو کم کرتے ہوئے اعلی کاٹنے کی درستگی حاصل کرنے کے طریقے تلاش کرنے کے لیے ان ٹیکنالوجیز کا مطالعہ کیا جا رہا ہے۔
تھرمل امپیکٹ ایریا اور کارکردگی پر اس کے اثرات
تھرمل کاٹنے کے عمل میں جیسے لیزر اور پلازما کٹنگ، زیادہ درجہ حرارت لامحالہ ویفر کی سطح پر تھرمل امپیکٹ زون بناتا ہے۔ یہ علاقہ، جہاں درجہ حرارت کا میلان نمایاں ہے، مواد کی خصوصیات کو تبدیل کر سکتا ہے، جس سے چپ کی حتمی کارکردگی متاثر ہوتی ہے۔
تھرمل متاثرہ زون (TAZ) کا اثر:
کرسٹل کی ساخت میں تبدیلیاں: زیادہ درجہ حرارت کے تحت، ویفر مواد کے اندر ایٹم دوبارہ ترتیب دے سکتے ہیں، جس سے کرسٹل کی ساخت میں بگاڑ پیدا ہوتا ہے۔ یہ مسخ مواد کو کمزور کر دیتا ہے، اس کی مکینیکل طاقت اور استحکام کو کم کرتا ہے، جس سے استعمال کے دوران چپ کی خرابی کا خطرہ بڑھ جاتا ہے۔
الیکٹریکل پراپرٹیز میں تبدیلیاں: زیادہ درجہ حرارت سیمی کنڈکٹر مواد میں کیریئر کی حراستی اور نقل و حرکت کو تبدیل کر سکتا ہے، جس سے چپ کی برقی چالکتا اور کرنٹ ٹرانسمیشن کی کارکردگی متاثر ہوتی ہے۔ یہ تبدیلیاں چپ کی کارکردگی میں کمی کا باعث بن سکتی ہیں، ممکنہ طور پر اسے اپنے مطلوبہ مقصد کے لیے غیر موزوں بناتی ہیں۔
ان اثرات کو کم کرنے کے لیے، کاٹنے کے دوران درجہ حرارت کو کنٹرول کرنا، کاٹنے کے پیرامیٹرز کو بہتر بنانا، اور کولنگ جیٹس یا پوسٹ پروسیسنگ ٹریٹمنٹ جیسے طریقے تلاش کرنا تھرمل اثر کی حد کو کم کرنے اور مواد کی سالمیت کو برقرار رکھنے کے لیے ضروری حکمت عملی ہیں۔
مجموعی طور پر، مائیکرو کریکس اور تھرمل امپیکٹ زون دونوں ویفر ڈائسنگ ٹیکنالوجی میں اہم چیلنجز ہیں۔ سیمی کنڈکٹر مصنوعات کے معیار کو بہتر بنانے اور ان کی مارکیٹ کی مسابقت کو بڑھانے کے لیے تکنیکی ترقی اور کوالٹی کنٹرول کے اقدامات کے ساتھ ساتھ مسلسل تحقیق ضروری ہو گی۔
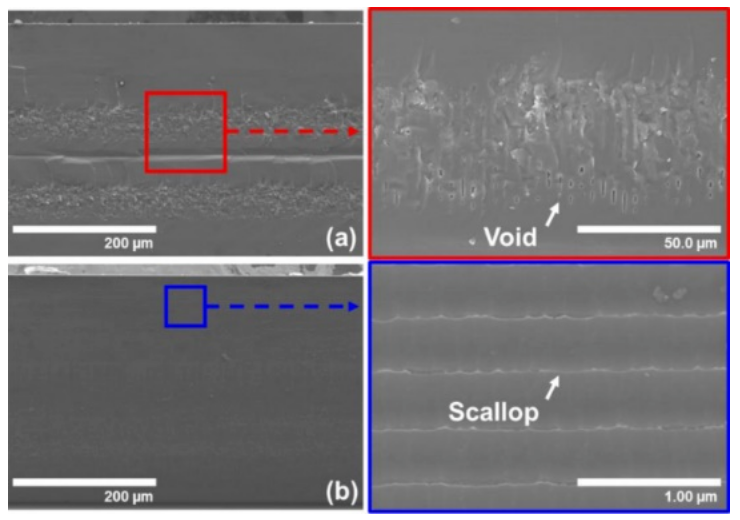
تھرمل امپیکٹ زون کو کنٹرول کرنے کے اقدامات:
کاٹنے کے عمل کے پیرامیٹرز کو بہتر بنانا: کاٹنے کی رفتار اور طاقت کو کم کرنے سے تھرمل امپیکٹ زون (TAZ) کے سائز کو مؤثر طریقے سے کم کیا جا سکتا ہے۔ اس سے کاٹنے کے عمل کے دوران پیدا ہونے والی گرمی کی مقدار کو کنٹرول کرنے میں مدد ملتی ہے، جس کا اثر براہ راست ویفر کی مادی خصوصیات پر پڑتا ہے۔
اعلی درجے کی کولنگ ٹیکنالوجیز: مائع نائٹروجن کولنگ اور مائیکرو فلائیڈک کولنگ جیسی ٹیکنالوجیز کا اطلاق تھرمل امپیکٹ زون کی حد کو نمایاں طور پر محدود کر سکتا ہے۔ ٹھنڈک کے یہ طریقے گرمی کو زیادہ مؤثر طریقے سے ختم کرنے میں مدد کرتے ہیں، اس طرح ویفر کی مادی خصوصیات کو محفوظ رکھتے ہیں اور تھرمل نقصان کو کم کرتے ہیں۔
مواد کا انتخاب: محققین نئے مواد کی تلاش کر رہے ہیں، جیسے کاربن نانوٹوبس اور گرافین، جو بہترین تھرمل چالکتا اور مکینیکل طاقت رکھتے ہیں۔ یہ مواد چپس کی مجموعی کارکردگی کو بہتر بناتے ہوئے تھرمل امپیکٹ زون کو کم کر سکتا ہے۔
خلاصہ یہ کہ، اگرچہ تھرمل امپیکٹ زون تھرمل کٹنگ ٹیکنالوجیز کا ناگزیر نتیجہ ہے، لیکن اسے بہتر طریقے سے پروسیسنگ تکنیک اور مواد کے انتخاب کے ذریعے کنٹرول کیا جا سکتا ہے۔ مستقبل کی تحقیق ممکنہ طور پر زیادہ موثر اور درست ویفر ڈائسنگ حاصل کرنے کے لیے فائن ٹیوننگ اور خودکار تھرمل کاٹنے کے عمل پر توجہ مرکوز کرے گی۔

توازن کی حکمت عملی:
ویفر کی پیداوار اور پیداواری کارکردگی کے درمیان بہترین توازن حاصل کرنا ویفر ڈائسنگ ٹیکنالوجی میں ایک مستقل چیلنج ہے۔ مینوفیکچررز کو ایک عقلی پیداواری حکمت عملی اور عمل کے پیرامیٹرز تیار کرنے کے لیے متعدد عوامل پر غور کرنے کی ضرورت ہے، جیسے کہ مارکیٹ کی طلب، پیداواری لاگت اور مصنوعات کے معیار۔ ایک ہی وقت میں، جدید ترین کٹنگ آلات متعارف کرانا، آپریٹر کی مہارتوں کو بہتر بنانا، اور خام مال کے کوالٹی کنٹرول کو بڑھانا پیداوار کی کارکردگی کو بڑھانے کے ساتھ ساتھ پیداوار کو برقرار رکھنے یا اس سے بھی بہتر بنانے کے لیے ضروری ہے۔
مستقبل کے چیلنجز اور مواقع:
سیمی کنڈکٹر ٹیکنالوجی کی ترقی کے ساتھ، ویفر کٹنگ کو نئے چیلنجز اور مواقع کا سامنا ہے۔ جیسے جیسے چپ کا سائز سکڑتا ہے اور انضمام میں اضافہ ہوتا ہے، درستگی اور معیار کو کاٹنے کے مطالبات نمایاں طور پر بڑھتے ہیں۔ اس کے ساتھ ساتھ، ابھرتی ہوئی ٹیکنالوجیز ویفر کاٹنے کی تکنیکوں کی ترقی کے لیے نئے آئیڈیاز فراہم کرتی ہیں۔ مینوفیکچررز کو مارکیٹ کی حرکیات اور تکنیکی رجحانات سے ہم آہنگ رہنا چاہیے، مارکیٹ کی تبدیلیوں اور تکنیکی تقاضوں کو پورا کرنے کے لیے پیداواری حکمت عملیوں اور عمل کے پیرامیٹرز کو مسلسل ایڈجسٹ اور بہتر بنانا چاہیے۔
آخر میں، مارکیٹ کی طلب، پیداواری لاگت، اور پروڈکٹ کے معیار کو مدنظر رکھ کر، اور جدید آلات اور ٹیکنالوجی متعارف کروا کر، آپریٹر کی مہارتوں کو بڑھا کر، اور خام مال کے کنٹرول کو مضبوط بنا کر، مینوفیکچررز ویفر ڈائسنگ کے دوران ویفر کی پیداوار اور پیداواری کارکردگی کے درمیان بہترین توازن حاصل کر سکتے ہیں، جس کے نتیجے میں موثر اور اعلیٰ معیار کی مصنوعات کی پیداوار سیمی کنڈکٹر ہوتی ہے۔
مستقبل کا آؤٹ لک:
تیز رفتار تکنیکی ترقی کے ساتھ، سیمی کنڈکٹر ٹیکنالوجی بے مثال رفتار سے ترقی کر رہی ہے۔ سیمی کنڈکٹر مینوفیکچرنگ میں ایک اہم قدم کے طور پر، ویفر کٹنگ ٹیکنالوجی دلچسپ نئی پیشرفت کے لیے تیار ہے۔ آگے دیکھتے ہوئے، ویفر کٹنگ ٹیکنالوجی سے سیمی کنڈکٹر انڈسٹری کی مسلسل ترقی میں نئی جان ڈالتے ہوئے، درستگی، کارکردگی اور لاگت میں نمایاں بہتری حاصل کرنے کی امید ہے۔
درستگی میں اضافہ:
اعلی درستگی کے حصول میں، ویفر کٹنگ ٹیکنالوجی موجودہ عمل کی حدود کو مسلسل آگے بڑھاتی رہے گی۔ کاٹنے کے عمل کے جسمانی اور کیمیائی طریقہ کار کا گہرائی سے مطالعہ کرنے اور کاٹنے کے پیرامیٹرز کو درست طریقے سے کنٹرول کرنے سے، سرکٹ ڈیزائن کی تیزی سے پیچیدہ ضروریات کو پورا کرنے کے لیے بہتر کاٹنے کے نتائج حاصل کیے جائیں گے۔ مزید برآں، نئے مواد کی تلاش اور کاٹنے کے طریقوں سے پیداوار اور معیار میں نمایاں بہتری آئے گی۔
کارکردگی میں اضافہ:
نئے ویفر کاٹنے کا سامان سمارٹ اور خودکار ڈیزائن پر توجہ مرکوز کرے گا۔ جدید کنٹرول سسٹمز اور الگورتھم کا تعارف آلات کو خود کار طریقے سے کٹنگ پیرامیٹرز کو مختلف مواد اور ڈیزائن کی ضروریات کو ایڈجسٹ کرنے کے قابل بنائے گا، اس طرح پیداواری کارکردگی میں نمایاں بہتری آئے گی۔ ملٹی ویفر کٹنگ ٹیکنالوجی اور تیز بلیڈ تبدیل کرنے کے نظام جیسی اختراعات کارکردگی کو بڑھانے میں اہم کردار ادا کریں گی۔
اخراجات کو کم کرنا:
ویفر کٹنگ ٹیکنالوجی کی ترقی کے لیے اخراجات کو کم کرنا ایک اہم سمت ہے۔ جیسا کہ نئے مواد اور کاٹنے کے طریقے تیار کیے جاتے ہیں، توقع کی جاتی ہے کہ سامان کے اخراجات اور دیکھ بھال کے اخراجات کو مؤثر طریقے سے کنٹرول کیا جائے گا۔ مزید برآں، پیداواری عمل کو بہتر بنانے اور سکریپ کی شرح کو کم کرنے سے مینوفیکچرنگ کے دوران فضلہ میں مزید کمی آئے گی، جس سے مجموعی پیداواری لاگت میں کمی واقع ہوگی۔
اسمارٹ مینوفیکچرنگ اور آئی او ٹی:
سمارٹ مینوفیکچرنگ اور انٹرنیٹ آف تھنگز (IoT) ٹیکنالوجیز کا انضمام ویفر کٹنگ ٹیکنالوجی میں تبدیلی لانے والی تبدیلیاں لائے گا۔ آلات کے درمیان انٹرکنیکٹیویٹی اور ڈیٹا شیئرنگ کے ذریعے، پیداواری عمل کے ہر قدم کو حقیقی وقت میں مانیٹر اور بہتر بنایا جا سکتا ہے۔ یہ نہ صرف پیداواری کارکردگی اور مصنوعات کے معیار کو بہتر بناتا ہے بلکہ کمپنیوں کو زیادہ درست مارکیٹ کی پیشن گوئی اور فیصلہ سازی میں معاونت فراہم کرتا ہے۔
مستقبل میں، ویفر کٹنگ ٹیکنالوجی درستگی، کارکردگی اور لاگت میں قابل ذکر ترقی کرے گی۔ یہ پیشرفت سیمی کنڈکٹر کی صنعت کی مسلسل ترقی کو آگے بڑھائے گی اور انسانی معاشرے میں مزید تکنیکی اختراعات اور سہولتیں لائے گی۔
پوسٹ ٹائم: نومبر-19-2024